鈦合金的熱處理方法
發(fā)布時(shí)間:
2024-07-29
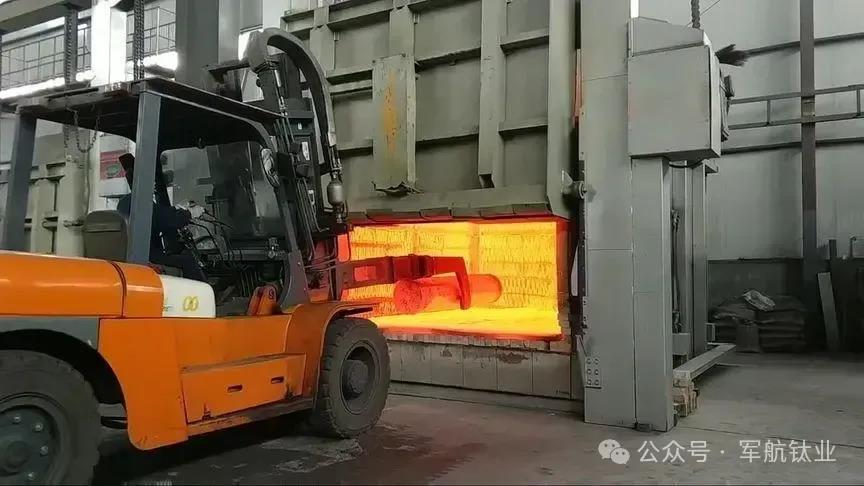
鈦合金的熱處理特點(diǎn)
(1)馬氏體相變不會(huì)使鈦合金的性能發(fā)生顯著變化。這個(gè)特點(diǎn)與鋼的馬 氏 體相變不同,鈦合金的熱處理強(qiáng)化只能依賴(lài)淬火形成的亞穩(wěn)相(包括馬氏體相)的時(shí)效分解,況且對(duì)于純a型鈦合金熱處理的方法基本上不能有效,即鈦合金的熱處理主要用于α+β型鈦合金。
(2)熱處理應(yīng)該避免形成ω相。形成ω相會(huì)使鈦合金變脆,正確選擇時(shí)效工藝(例如,采用較高的時(shí)效溫度)即可使ω相分解。
(3)利用反復(fù)相變難于細(xì)化鈦合金晶粒。這一點(diǎn)也不同于鋼鐵材料,大多數(shù)的鋼可以利用奧氏體與珠光體(或鐵素體、滲碳體)的反復(fù)相變控制新相形核與長(zhǎng)大,達(dá)到晶粒細(xì)化的目的,而鈦合金中沒(méi)有這樣的現(xiàn)象。
(4)導(dǎo)熱性差。導(dǎo)熱性差可導(dǎo)致鈦合金,尤其是α+β鈦合金的淬透性差,淬火熱應(yīng)力大,淬火時(shí)零件易翹曲。由于導(dǎo)熱性差,鈦合金變形時(shí)易引起局部溫升過(guò)高,使局部溫度有可能超過(guò)β轉(zhuǎn)變點(diǎn)而形成魏氏組織。
(5)化學(xué)性活潑。熱處理時(shí),鈦合金易與氧和水蒸氣反應(yīng),在工件表面形成具有一定深度的富氧層或氧化皮,使合金的性能降低。同時(shí)鈦合金熱處理時(shí)容易吸氫,引起氫脆。
(6)β轉(zhuǎn)變點(diǎn)差異大。即使是同一成分,但由于冶煉爐次的不同,其β轉(zhuǎn)變溫度有時(shí)差別很大。
(7)在β相區(qū)加熱時(shí),β晶粒長(zhǎng)大傾向大。β晶粒粗化可使合金塑性急劇下降,故應(yīng)嚴(yán)格控制加熱的溫度和時(shí)間,并慎用在β相區(qū)加熱的熱處理。
合金的熱處理類(lèi)型
鈦合金的相變是鈦合金熱處理的基礎(chǔ),為了改善鈦合金的性能,除采用合理的合金化外,還要配合適當(dāng)?shù)臒崽幚聿拍軐?shí)現(xiàn)。鈦合金的熱處理種類(lèi)較多,常用的有退火處理、時(shí)效處理、形變熱處理和化學(xué)熱處理等。
01
退火處理
退火適用于各種鈦合金,其主要目的是消除應(yīng)力,提高合金塑性及穩(wěn)定組織。退火的形式包括去應(yīng)力退火、再結(jié)晶退火、雙重退火、等溫退火和真空退火等,鈦合金各種方式退火溫度范圍如圖1所示。
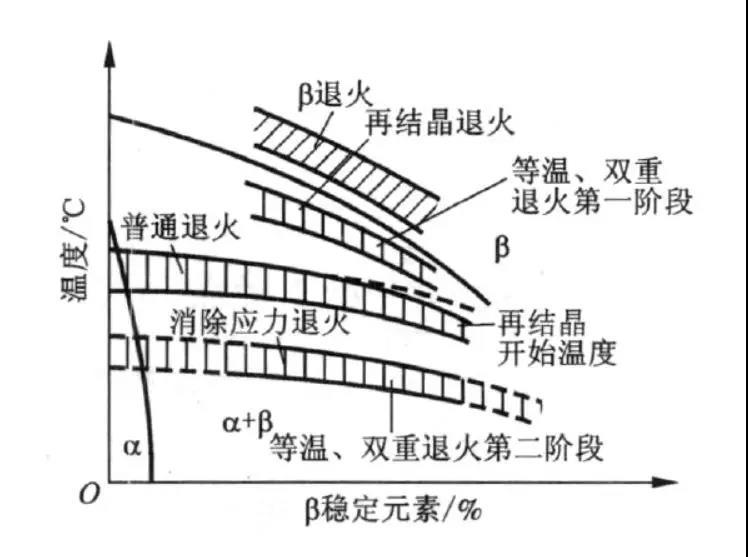
圖1 鈦合金各方式退火溫度范圍示意圖
(1)去應(yīng)力退火。為了消除鑄造、冷變形及焊接等工藝過(guò)程中產(chǎn)生的內(nèi)應(yīng)力,可采用去應(yīng)力退火。去應(yīng)力退火的溫度應(yīng)低于再結(jié)晶溫度,一般為450~650℃,所需的時(shí)間取決于工件的截面尺寸、加工歷史及所需消除應(yīng)力的程度。
(2)普通退火。其目的是使鈦合金半成品消除基本應(yīng)力,并具有較高的強(qiáng)度和符合技術(shù)條件要求的塑性。退火溫度一般與再結(jié)晶開(kāi)始溫度相當(dāng)或略低,此種退火工藝一般冶金產(chǎn)品出廠(chǎng)時(shí)使用,所以又可以稱(chēng)為工廠(chǎng)退火。
(3)完全退火。目的是完全消除加工硬化,穩(wěn)定組織和提高塑性。這一過(guò)程主要發(fā)生再結(jié)晶,故亦稱(chēng)再結(jié)晶退火。退火溫度最好介于再結(jié)晶溫度和相變溫度之間,如果超過(guò)了相變溫度會(huì)形成魏氏組織而使合金的性能惡化。對(duì)于各種不同種類(lèi)的鈦合金,退火的類(lèi)型、溫度和冷卻方式均不同。
(4)雙重退火。為了改善合金的塑性、斷裂韌性和穩(wěn)定組織可采用雙重退火。退火后的合金組織更加均勻和接近平衡狀態(tài)。耐熱鈦合金為了保證在高溫及長(zhǎng)期應(yīng)力作用下組織和性能的穩(wěn)定,常采用此類(lèi)退火。雙重退火是對(duì)合金進(jìn)行兩次加熱和空冷。第一次高溫退火加熱溫度高于或接近再結(jié)晶終了溫度,使再結(jié)晶充分進(jìn)行,又不使晶粒明顯長(zhǎng)大,并控制ap相的體積分?jǐn)?shù)。空冷后組織還不夠穩(wěn)定,需進(jìn)行第二次低溫退火,退火溫度低于再結(jié)晶溫度,保溫較長(zhǎng)時(shí)間,使高溫退火得到的亞穩(wěn)β相充分分解。
(5)等溫退火。等溫退火可獲得最好的塑性和熱穩(wěn)定性。此種退火適用于β穩(wěn)定元素含量較高的雙相鈦合金。等溫退火采用分級(jí)冷卻的方式,即加熱至再結(jié)晶溫度以上保溫后,立即轉(zhuǎn)入另一較低溫度的爐中(一般600~650℃)保溫,而后空冷至室溫。
02
淬火處理
淬火時(shí)效是鈦合金熱處理強(qiáng)化的主要方式,利用相變產(chǎn)生強(qiáng)化效果,故又稱(chēng)強(qiáng)化熱處理。鈦合金熱處理的強(qiáng)化效果決定于合金元素的性質(zhì)、濃度及熱處理規(guī)范,因?yàn)檫@些因素影響合金淬火所得的亞穩(wěn)定相的類(lèi)型、成分、數(shù)量和分布,以及亞穩(wěn)定相分解過(guò)程中析出相的本質(zhì)、結(jié)構(gòu)、彌散程度等,而這些又與合金的成分、熱處理工藝規(guī)范和原始組織有關(guān)。
對(duì)于成分一定的合金,時(shí)效強(qiáng)化效果取決于所選的熱處理工藝。淬火溫度越高,時(shí)效強(qiáng)化效果越明顯,但高于β轉(zhuǎn)變溫度淬火,由于晶粒過(guò)分粗大而導(dǎo)致脆性。對(duì)于濃度較低的兩相鈦合金可采用較高溫度淬火,以獲得更多的馬氏體,而濃度較高的兩相鈦合金則選用較低溫度淬火,以得到較多的亞穩(wěn)β相,這樣可以獲得最大的時(shí)效強(qiáng)化效果。冷卻方式一般選用水冷或者油冷,淬火的過(guò)程要迅速,以防止β相在轉(zhuǎn)移過(guò)程中發(fā)生分解,降
低時(shí)效強(qiáng)化效果。時(shí)效溫度和時(shí)間的選擇應(yīng)以獲得最好的綜合性能為準(zhǔn)則,一般α+β型鈦合金時(shí)效溫度為500~600℃,時(shí)間4~12h;而β型鈦合金的時(shí)效溫度為450~550℃,時(shí)間8~24h,冷卻方式均采用空冷。
03
形變熱處理
形變熱處理是將壓力加工(鍛、軋等)與熱處理工藝有效地結(jié)合起來(lái),可同時(shí)發(fā)揮形變強(qiáng)化與熱處理強(qiáng)化的作用,得到與單一的強(qiáng)化方法所不能獲得的組織與綜合性能。常見(jiàn)的形變熱處理工藝如圖2所示。不同類(lèi)型的形變熱處理按照變形溫度與再結(jié)晶溫度和相轉(zhuǎn)變溫度的關(guān)系進(jìn)行分類(lèi),按變形溫度分為:
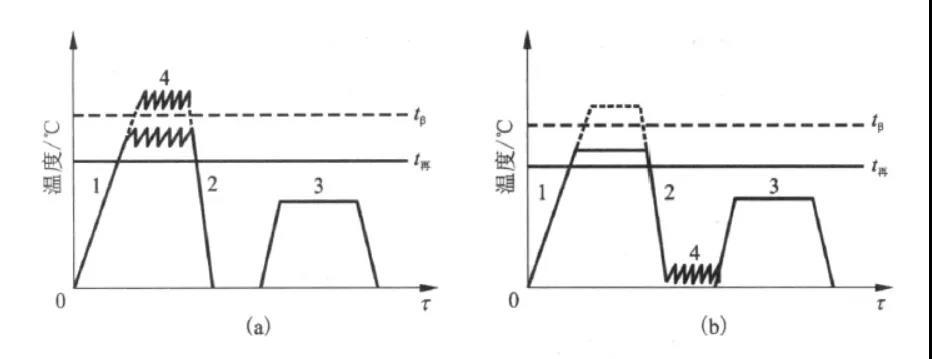
圖2 鈦合金的形變熱處理工藝過(guò)程示意
(a)高溫形變熱處理;(b)低溫形變熱處理
1-加熱;2-水冷;3-時(shí)效;4-高或低溫變形;tβ-β相變點(diǎn);t再-再結(jié)晶溫度
(1)高溫形變熱處理。加熱到再結(jié)晶溫度以上,變形40%~85%后迅速淬火,再進(jìn)行常規(guī)的時(shí)效熱處理。
(2)低溫形變熱處理。在再結(jié)晶溫度以下進(jìn)行變形50%左右,隨后再進(jìn)行常規(guī)的時(shí)效處理。
(3)復(fù)合形變熱處理。將高溫形變熱處理和低溫形變熱處理結(jié)合起來(lái)的一種工藝。
04
化學(xué)熱處理
鈦合金的摩擦系數(shù)較大,耐磨性差(一般比鋼約低40%),在接觸表面上容易產(chǎn)生黏結(jié),引起摩擦腐蝕。在氧化介質(zhì)中鈦合金的耐腐蝕性較強(qiáng),但在還原介質(zhì)(鹽酸、硫酸等)中的抗腐蝕性較差。為了改善這些性能,可采用電鍍、噴涂和化學(xué)熱處理(滲氮、滲氧等)等方法。滲氮后的氮化層硬度比未氮化時(shí)表層高2~4倍,因而明顯提高合金的耐磨性,同時(shí)還改善合金在還原性介質(zhì)中的抗蝕性;滲氧可將合金耐蝕性提高7~9倍,但合金的塑性和疲勞強(qiáng)度會(huì)有不同程度的損失
真空熱處理
由于鈦異常活潑,很容易受碳、氧、氫、氧的污染,使合金性能變壞,所以鈦合金熱處理時(shí)應(yīng)采用真空爐或氬氣保護(hù);如果在氧化性氣氛中加熱,則應(yīng)嚴(yán)格控制和去除工件表面氧化層。需要進(jìn)行真空熱處理的鈦合金零件也越來(lái)越多,除了通常進(jìn)行的鈦合金鈑金件和鑄件的去應(yīng)力退火、鈦合金緊固標(biāo)準(zhǔn)件的固溶處理和時(shí)效處理、鈦合金的除氫退火均需在真空爐中進(jìn)行以外,高強(qiáng)度鈦合金鈑金零件的約束時(shí)效處理也必須在真空爐中進(jìn)行。真空熱處理是鈦合金零件制造過(guò)程中的關(guān)鍵工序,其最終性能在很大程度上取決于熱處理的正確進(jìn)行。
真空熱處理的一個(gè)主要參數(shù)是真空工作壓強(qiáng),航空工業(yè)標(biāo)準(zhǔn)規(guī)定:在真空退火過(guò)程中,為避免因真空壓強(qiáng)過(guò)低而產(chǎn)生真空表面腐蝕,一般應(yīng)將真空工作壓強(qiáng)控制在不小于2×10-3Pa。也有采用高純氬氣進(jìn)行分壓控制的。
惰性氣體可以作為保護(hù)性氣氛的加熱介質(zhì),也可用于真空固溶處理時(shí)的淬火介質(zhì)。由于鈦的化學(xué)活性比較高,所以對(duì)于氬氣的純度也有更高的要求。純度不小于99.99%的純氬一般不適用于鈦合金的熱處理。國(guó)外標(biāo)準(zhǔn)中規(guī)定了對(duì)惰性氣體(氦和氬)的露點(diǎn)要求為不高于-54℃。航標(biāo)規(guī)定采用符合GB/T10624的高純氬,純度不小于99.999%。
國(guó)內(nèi)外的有關(guān)標(biāo)準(zhǔn)均未對(duì)真空爐熱處理后工件的出爐溫度做出規(guī)定,航標(biāo)規(guī)定了真空熱處理后工件應(yīng)在200℃以下出爐空冷。在惰性氣體或真空中加熱的鈦件表面出現(xiàn)淡黃色氧化膜時(shí)可不清除;若零件表面存在淡藍(lán)色、藍(lán)色或灰色氧化膜時(shí)必須按空氣爐規(guī)定清除。
固溶處理淬火允許延遲時(shí)間
鈦合金固溶處理加熱完成后的冷卻要嚴(yán)格按淬火要求進(jìn)行,如果冷速過(guò)低,合金的相成分發(fā)生明顯擴(kuò)散,將嚴(yán)重影響時(shí)效強(qiáng)化效果。通常鈦合金工件淬火允許的延遲時(shí)間必須符合表1的要求。
表1 鈦合金最長(zhǎng)淬火延遲時(shí)間
加熱時(shí)間/h | |||||||
≤0.2 | 0.2~0.5 | 0.5~1 | 1~2 | 2~6 | 6~10 | 10~20 | |
500~600 | 不要求 | 8 | 13 | 13 | 13 | 25 | 51 |
600~700 | 8 | 13 | 25 | 25 | 51 | 76 | 76 |
700~760 | 13 | 25 | 25 | 51 | 76 | 76 | 152 |
760~820 | 25 | 25 | 51 | 76 | 142 | 152 | |
820~930 | 51 | 76 | 142 | 152 | 254 | — | — |
930~980 | 76 | 142 | 152 | 254 | — | — | — |
980~1100 | 152 | 254 | 356 | — | — | — | — |
鈦合金在空氣電爐加熱氧化層去除
鈦合金半成品、零件、結(jié)構(gòu)件的熱處理可以在電爐中加熱,但不應(yīng)在氣體火焰爐或重油爐中加熱。鈦合金件表面的氧化層必須清除,其清除方法包括酸洗、化學(xué)銑切、噴砂或機(jī)加工等。鈦合金的精加工件表面的氧化層去除后,還應(yīng)根據(jù)規(guī)定清除一定厚度的基體金屬,其具體參數(shù)見(jiàn)表2。
表2 去除基體金屬最小深度
加熱溫度/℃ | 加熱時(shí)間/h | ||||||
≤0.2 | 0.2~0.5 | 0.5~1 | 1~2 | 2~6 | 6~10 | 10~20 | |
500~600 | 不要求 | 8 | 13 | 13 | 13 | 25 | 51 |
600~700 | 8 | 13 | 25 | 25 | 51 | 76 | 76 |
700~760 | 13 | 25 | 25 | 51 | 76 | 76 | 152 |
760~820 | 25 | 25 | 51 | 76 | 142 | 152 | |
820~930 | 51 | 76 | 142 | 152 | 254 | — | — |
930~980 | 76 | 142 | 152 | 254 | — | — | — |
980~1100 | 152 | 254 | 356 | — | — | — | — |
注:在進(jìn)行多道次加熱時(shí),可在最后一道加熱后消除氧化層,加熱時(shí)間以各次相加計(jì)算。
本文系網(wǎng)絡(luò)轉(zhuǎn)載,版權(quán)歸原作者所有。但因轉(zhuǎn)載眾多,無(wú)法確認(rèn)真正原始作者,故僅表明轉(zhuǎn)載來(lái)源。如涉及作品版權(quán)問(wèn)題,請(qǐng)與我們聯(lián)系,我們將根據(jù)您提供的版權(quán)證明材料確認(rèn)版權(quán)并刪除內(nèi)容!本文內(nèi)容為原作者觀(guān)點(diǎn),并不代表本公眾號(hào)贊同其觀(guān)點(diǎn)和對(duì)其真實(shí)性負(fù)責(zé)。
最新資訊